Through a study of natural processes at the molecular level, we’ve discovered that these processes inherently evolve along energetically favorable pathways, leading to remarkable efficiency. Embracing this principle, our institute places a strong emphasis on efficiency and minimizing energy consumption. We draw inspiration from nature’s intrinsic effectiveness and strive to incorporate these principles into our building.
Our building design is deeply inspired by “earthship” architecture, a visionary concept pioneered by visionary architect Michael Reynolds. Reynolds dedicated his life to constructing homes from recycled materials, completely independent of conventional engineering networks. His pioneering work has garnered recognition for developing self-sustainable, eco-friendly housing deeply rooted in harmony with nature. We hold profound appreciation for his architectural style and principles, marked by a commitment to simplicity, natural minimalism, and the maximal utilization of local and natural materials.
In our building, we’ve adapted the iconic U-shape characteristic of earthship design, complemented by a dominant south-facing glass wall. To enhance temperature control and act as a windbreak, we’ve added a small greenhouse in front of this wall. However, we’ve made notable departures from Reynolds’ original design, particularly in the area of insulation and our building’s subterranean placement.
The decision to construct our building entirely underground was primarily driven by aesthetic considerations. Yet, this choice necessitated additional insulation. The advantages of an underground structure lie in the relatively stable soil temperatures that hover around 8°C throughout the year. This ensures a naturally cool interior during scorching summers, even when external temperatures exceed 37°C. Moreover, it guarantees a frost-free environment in the winter. However, active heating is required to maintain comfort during colder months, hence the importance of insulation to retain heat efficiently.
In terms of construction, we began by excavating a U-shaped hole in the ground. At the base, we placed a layer of extruded polystyrene (similar to what we used for the walls), followed by a hydro-isolation layer and a 10cm layer of concrete. The walls were constructed using the tire method characteristic of earthship structures, incorporating approximately 300 tires filled with soil. The walls were then enveloped by a 20cm layer of polystyrene insulation for thermal efficiency. A vapor barrier (nop foil) serves as a supplementary hydro-isolation layer. Surprisingly, despite its seemingly minimal thickness, our hydro-isolation layer has effectively prevented moisture from infiltrating the walls. Our location on a hill with no underground water and the tire walls acting as a water barrier have contributed to this success.
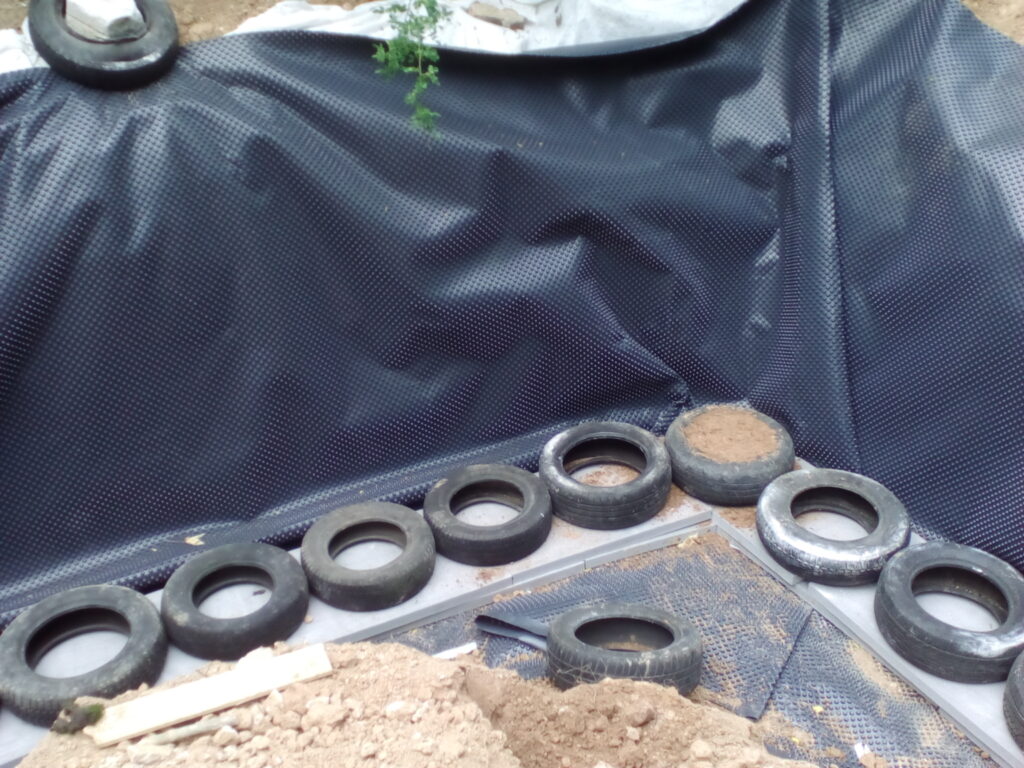
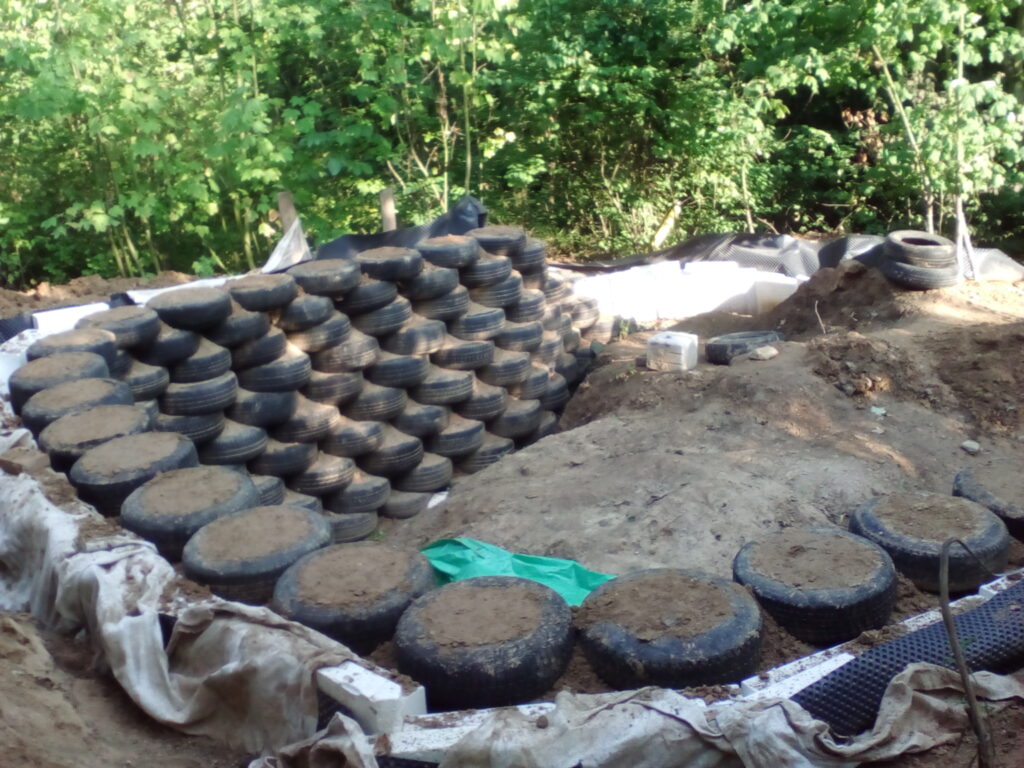
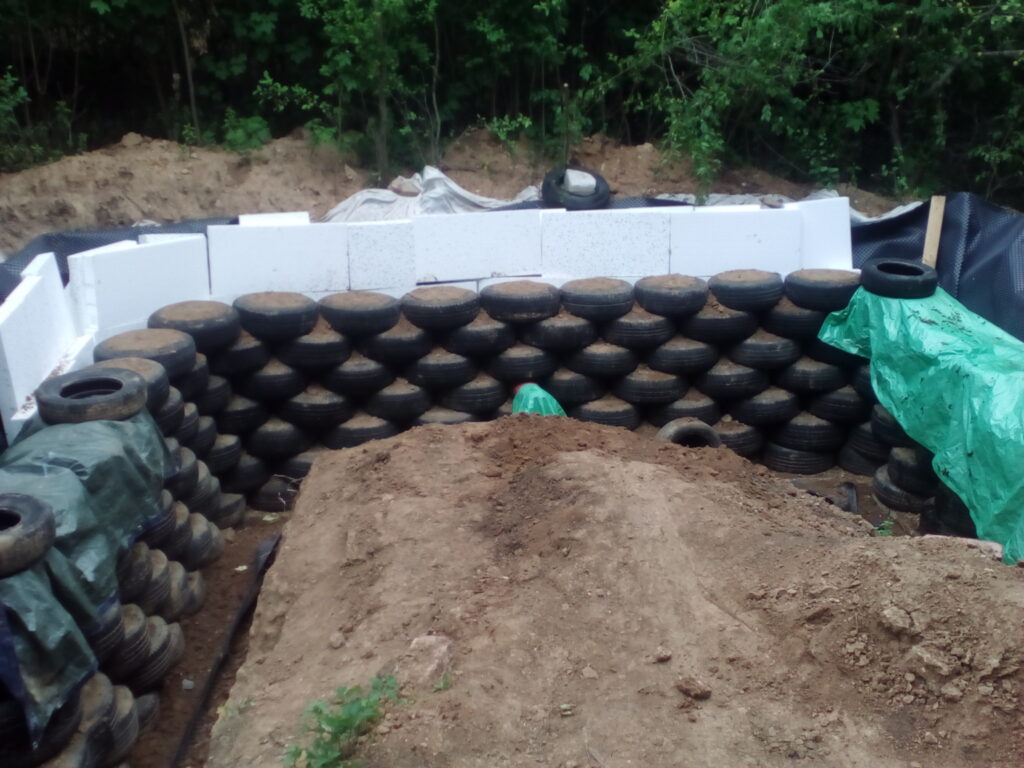
Although moisture is not a concern through the walls, our underground setting does result in higher humidity levels. Since our main room lacks other windows for natural air circulation, we rely on external ventilation systems to maintain air quality (details provided in the “Technology Focus” section).
While our building embodies sustainability and simplicity, one aspect we view as a potential weakness is the roof design. We adopted a design inspired by Michael Reynolds’ early work and constructed a wooden roof supported by wooden beams. The aesthetic appeal of this design is undeniable, but it comes with a drawback—simplicity.
Directly atop the roof boards, we’ve applied a layer of tar pitch. This layer serves as a moisture barrier, preventing any moisture from the interior space from penetrating the roof wood. Following the roof’s hydro-isolation, there’s a thick layer of polystyrene for thermal insulation. This is followed by a vapor barrier (nop foil) and topped with a relatively thin 10-15 cm layer of soil. While this design serves its purpose, we acknowledge that the construction details could be improved.
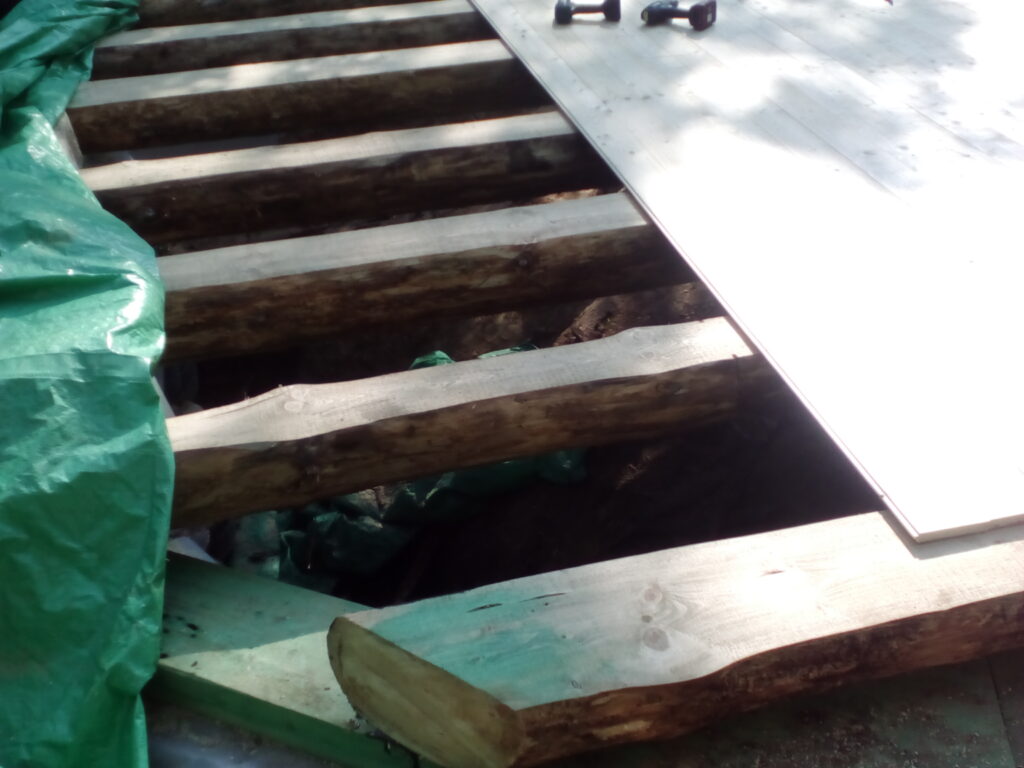
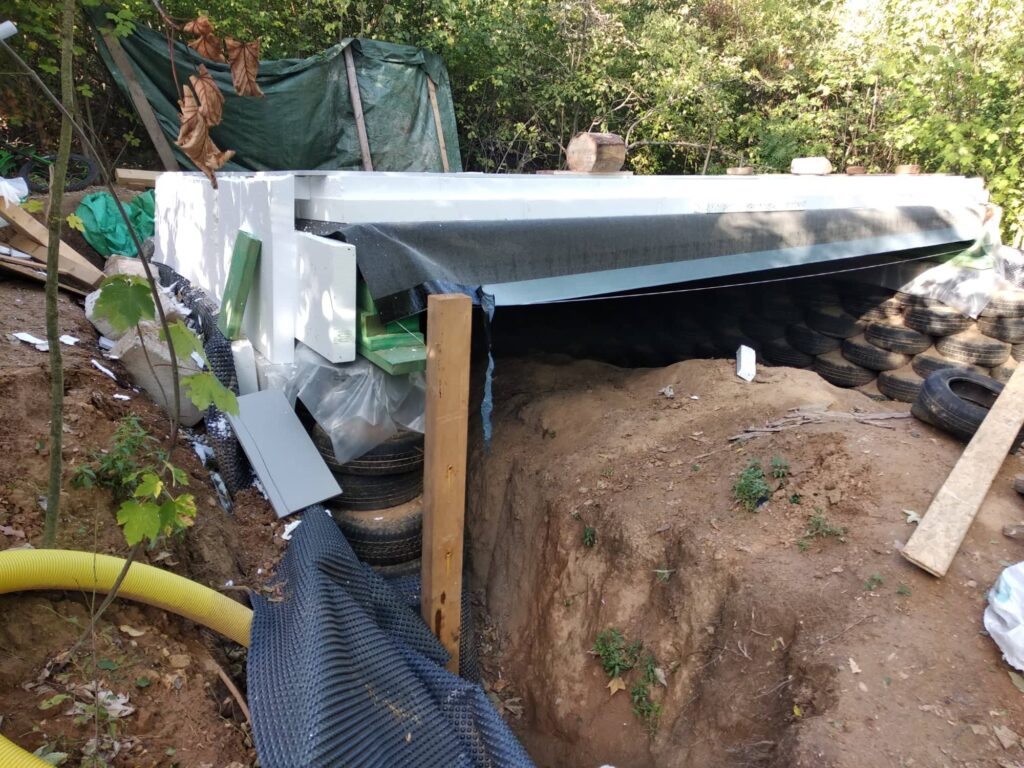
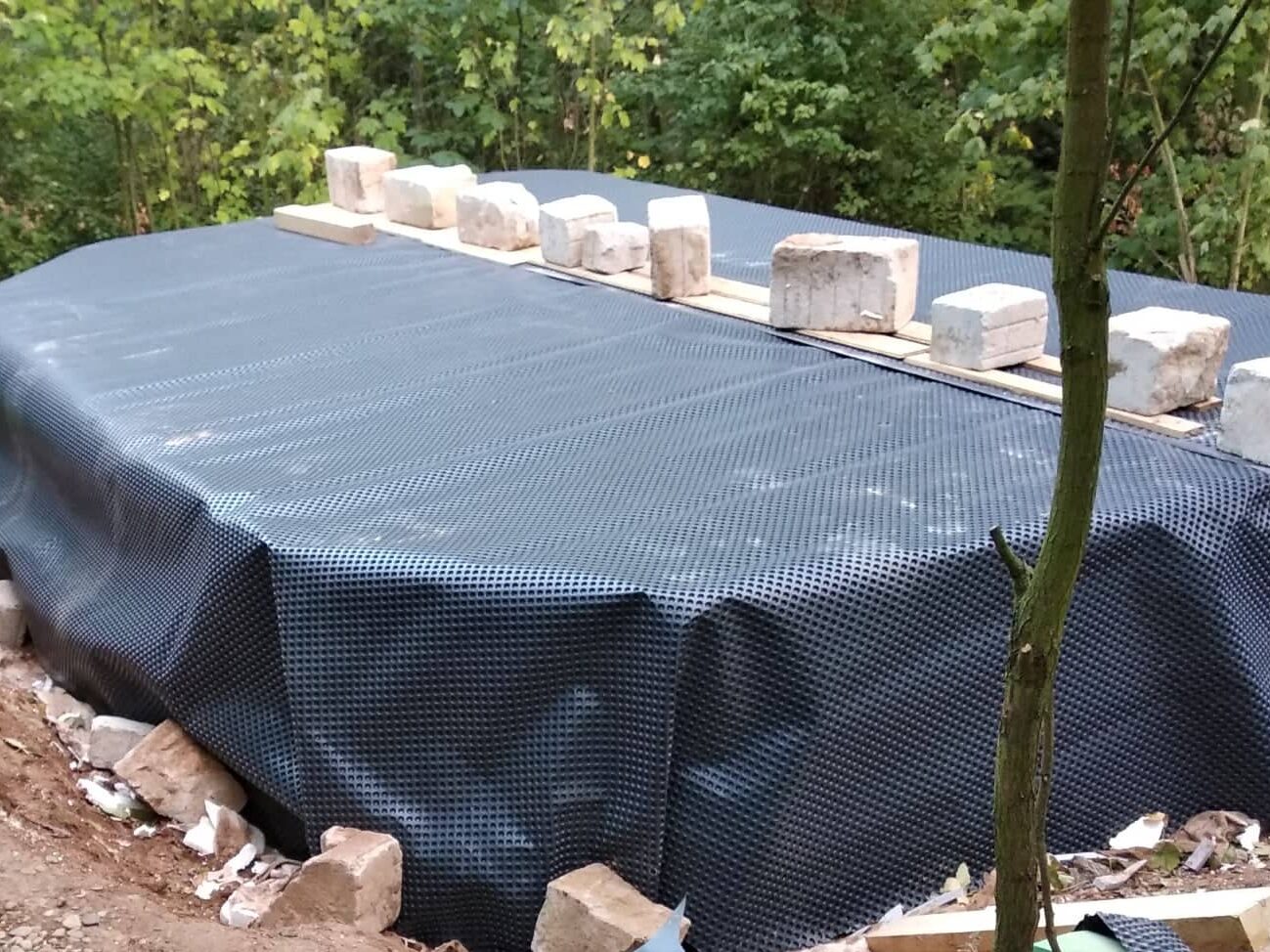
In addition to construction details, we face challenges from the natural environment. Rodents, particularly mice, pose a vulnerability to the roof. They have the ability to infiltrate the hydro-isolation layer, potentially causing issues. As a result, we anticipate the need for roof reconstruction in the coming years to address these challenges and enhance the overall integrity of our structure.
The fundamental principle of Earthship design involves a direct connection to the surrounding environment, resulting in the absence of heat insulation in both the walls and the floor. However, we have diverged from this approach due to the necessity of insulation in our specific geographical position. The composition of the institute’s floor includes a layer of gravel covered by a tar belt to manage moisture evaporating from the ground. Directly above the tar, there is a 10 cm layer of extruded polystyrene, a thin polyethylene foil, and a 10 cm layer of concrete. The floor is then finished with tiles.
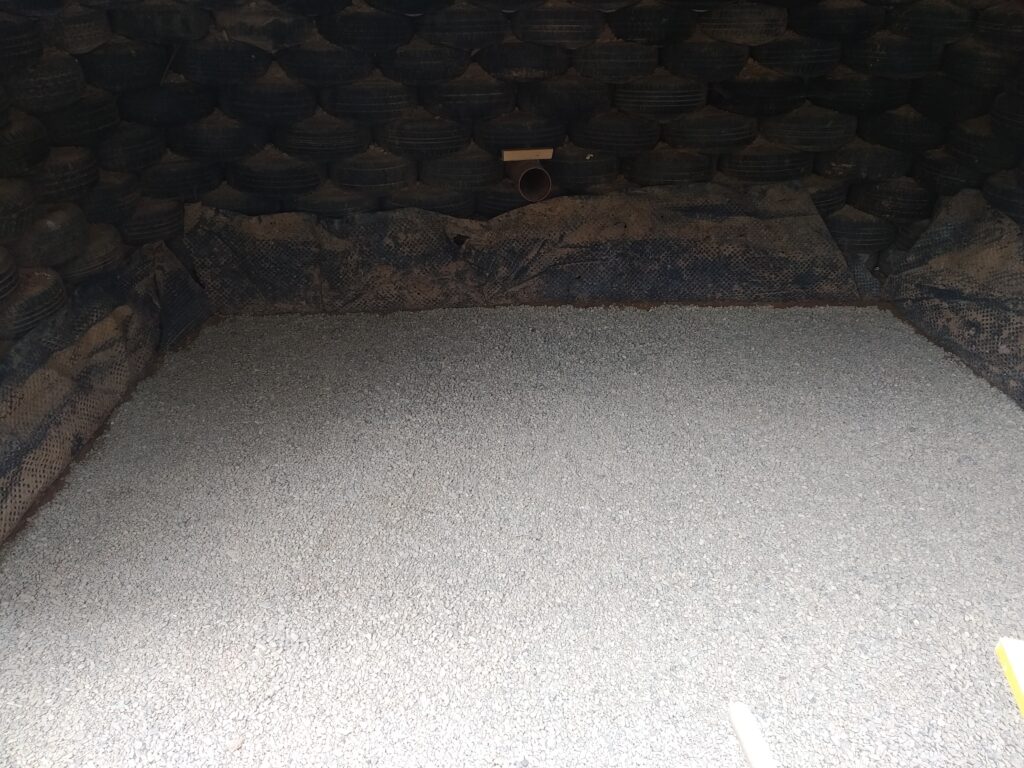
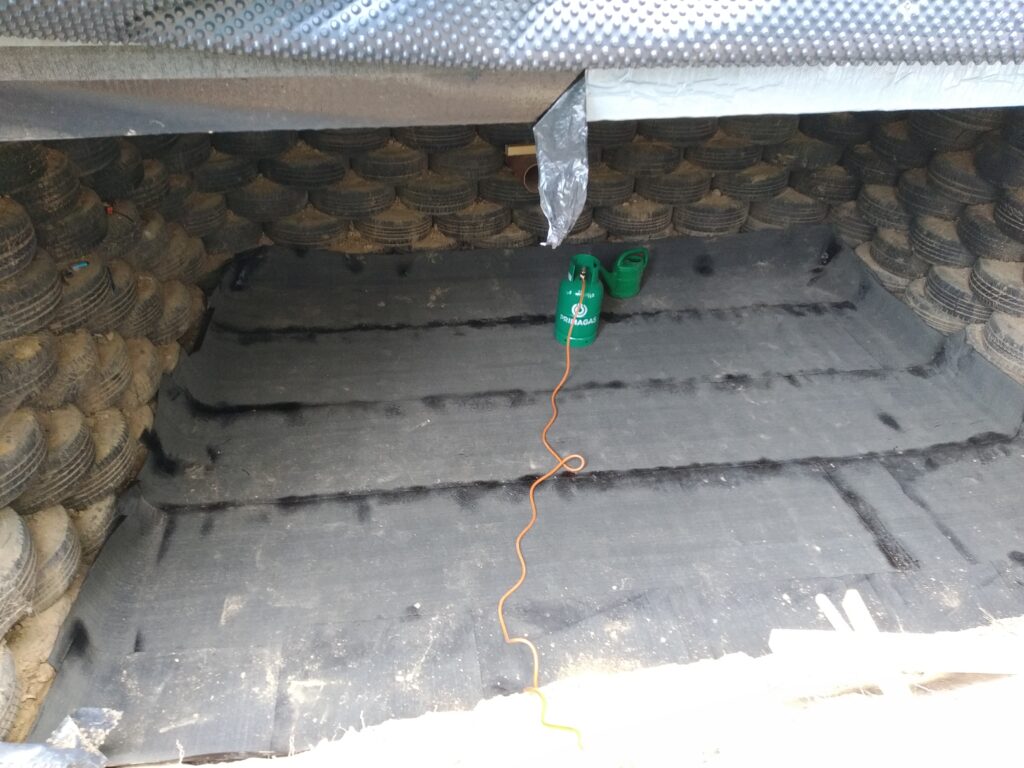
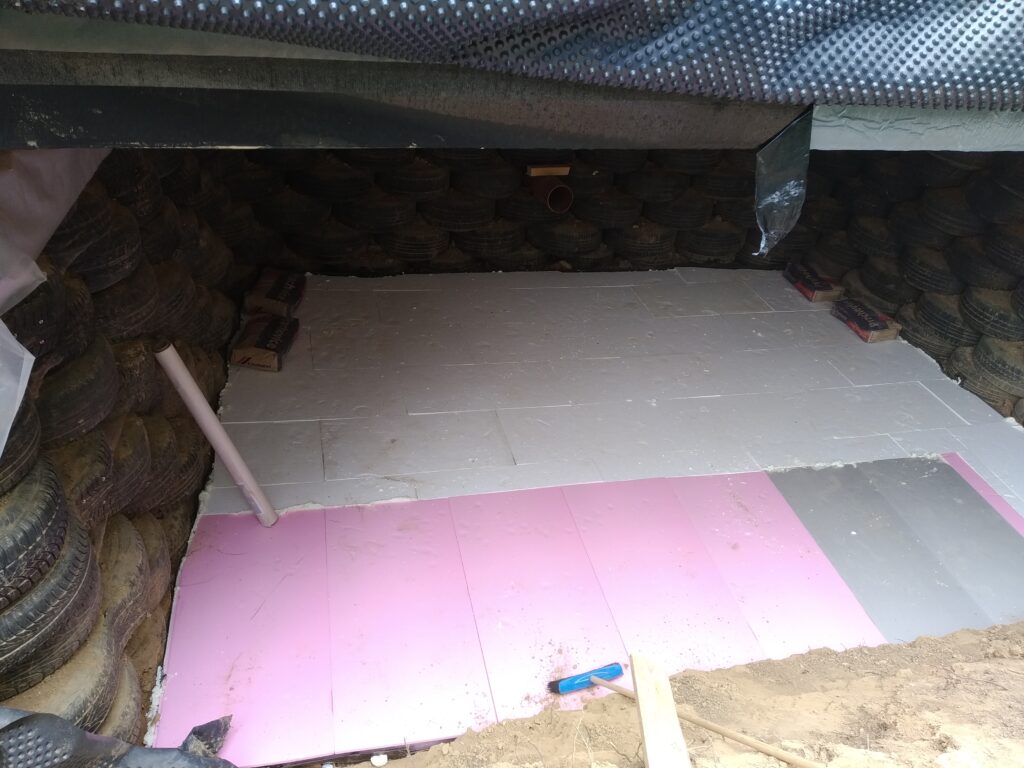
The south-facing wall of the institute is formed by a greenhouse, the sole open side that allows sunlight into the interior. We’ve established a separation between the greenhouse and the interior using another glass wall composed of two-layered glass windows. This design turns the greenhouse into a heat buffer, facilitating the cultivation of vegetables.
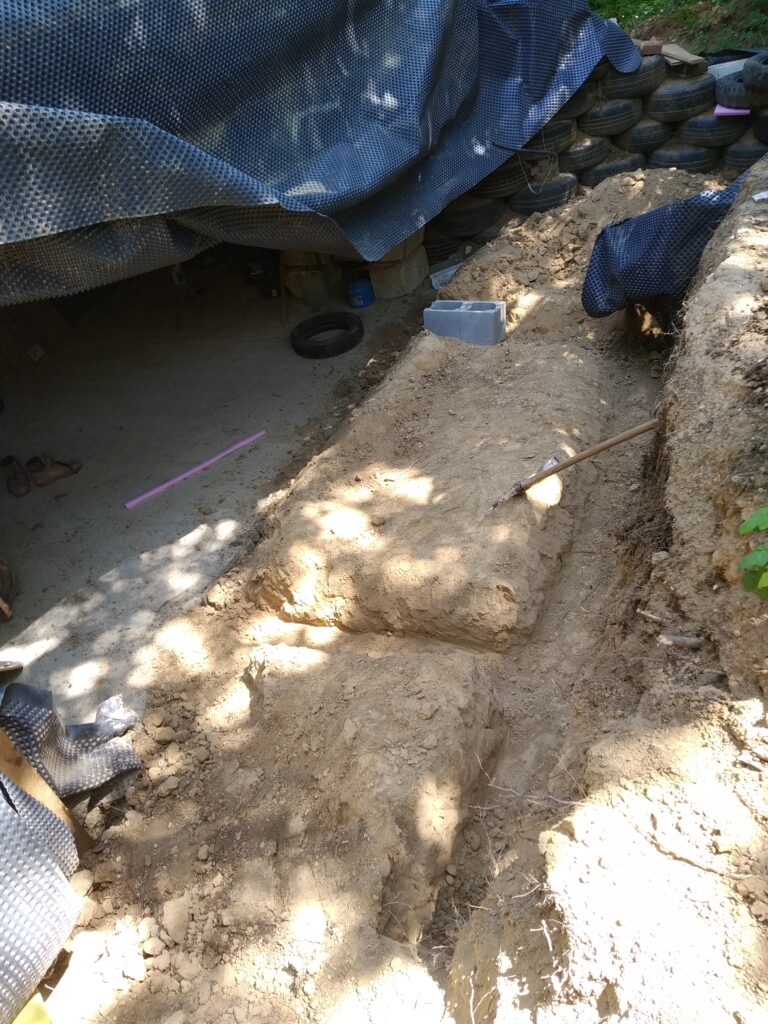

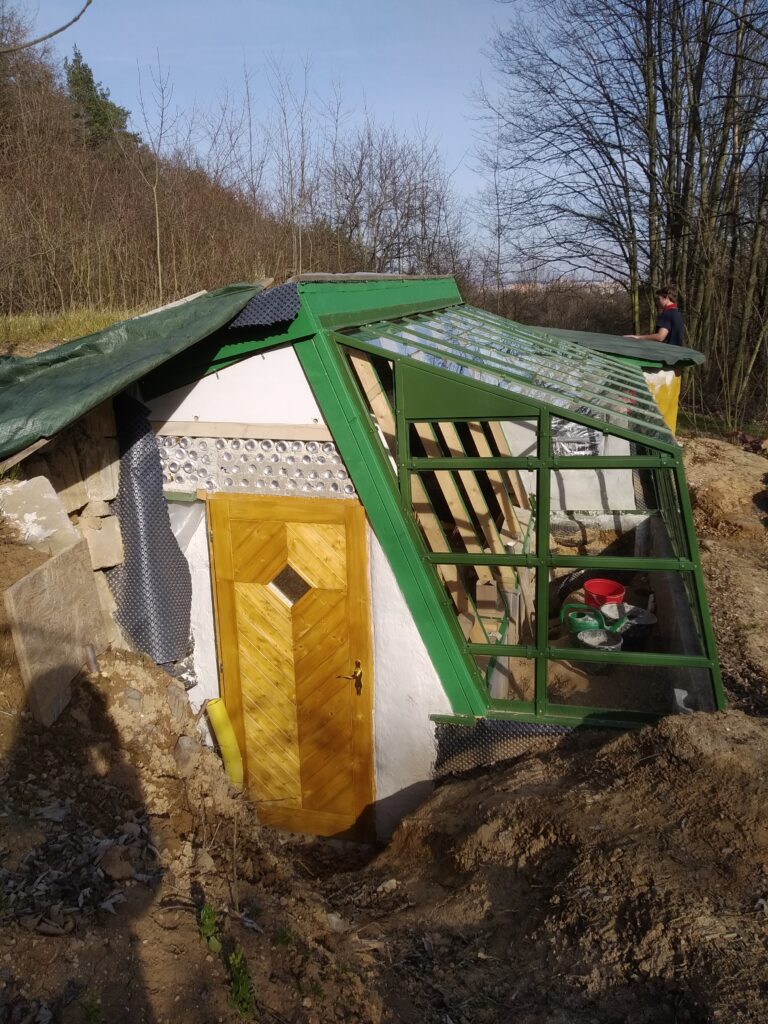
All the interior wall finishes have been achieved using clay sourced during construction. Multiple layers of clay are applied to the tire wall for finalization. The first layer is quite rough and consists solely of clay to fill the gaps between the tires. Each layer needs to dry before proceeding with the next layer, taking an average of three weeks, depending on layer thickness and environmental conditions. The subsequent layer is still relatively rough and can also consist of pure clay. Its purpose is to smooth out the holes before the application of the final layer. To enhance the firmness of the final layer, a mesh is placed on the wall for support. In the last layer, clay must be mixed with sand to prevent cracks during drying. The composition of the clay:sand mixture depends on the local clay and can range from 1:1 to 1:4. For our purpose, a ratio of 1:2 serves the intended purpose. Cut straw was added to the mixture to enhance the coherence of the final layer.
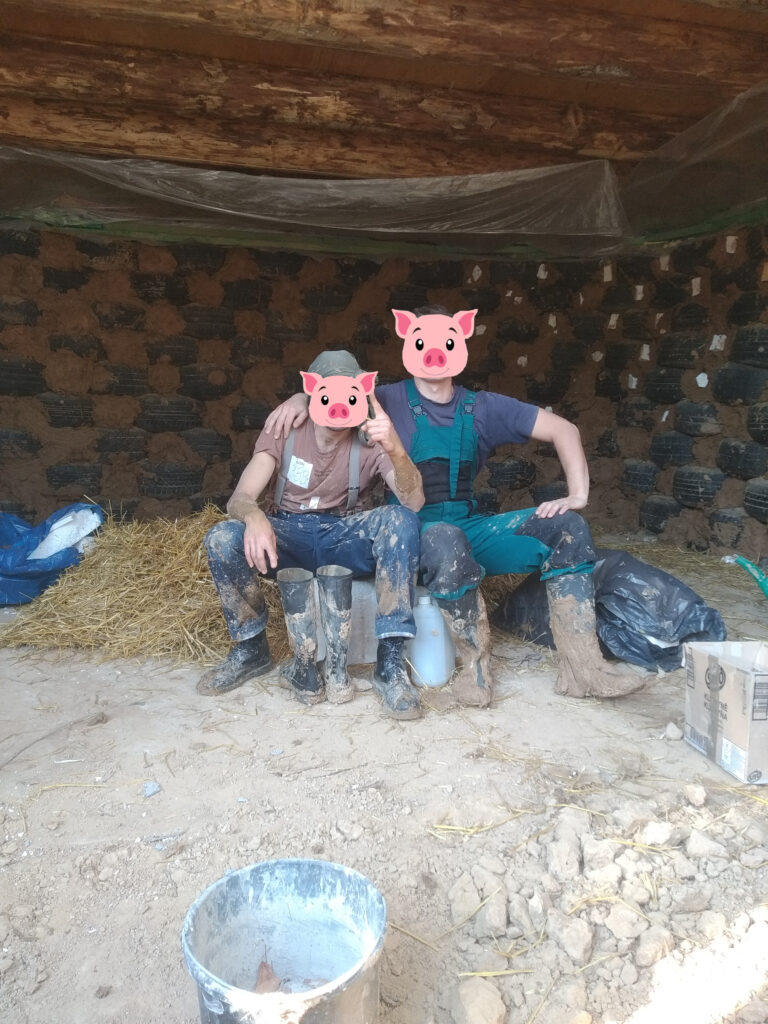
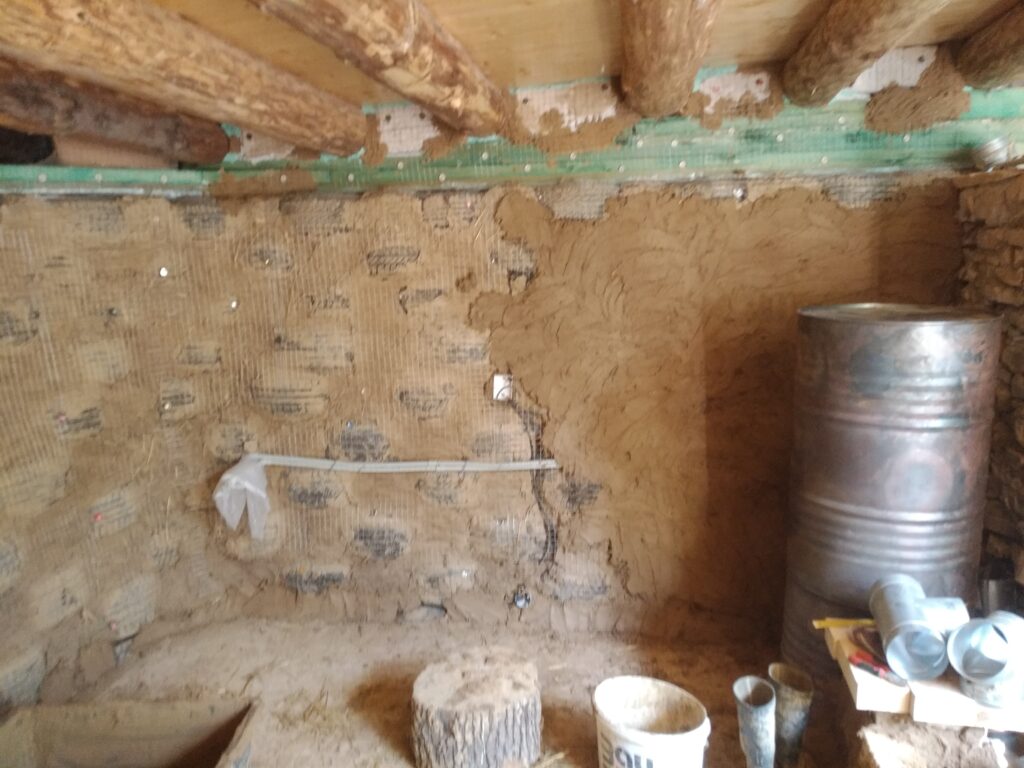
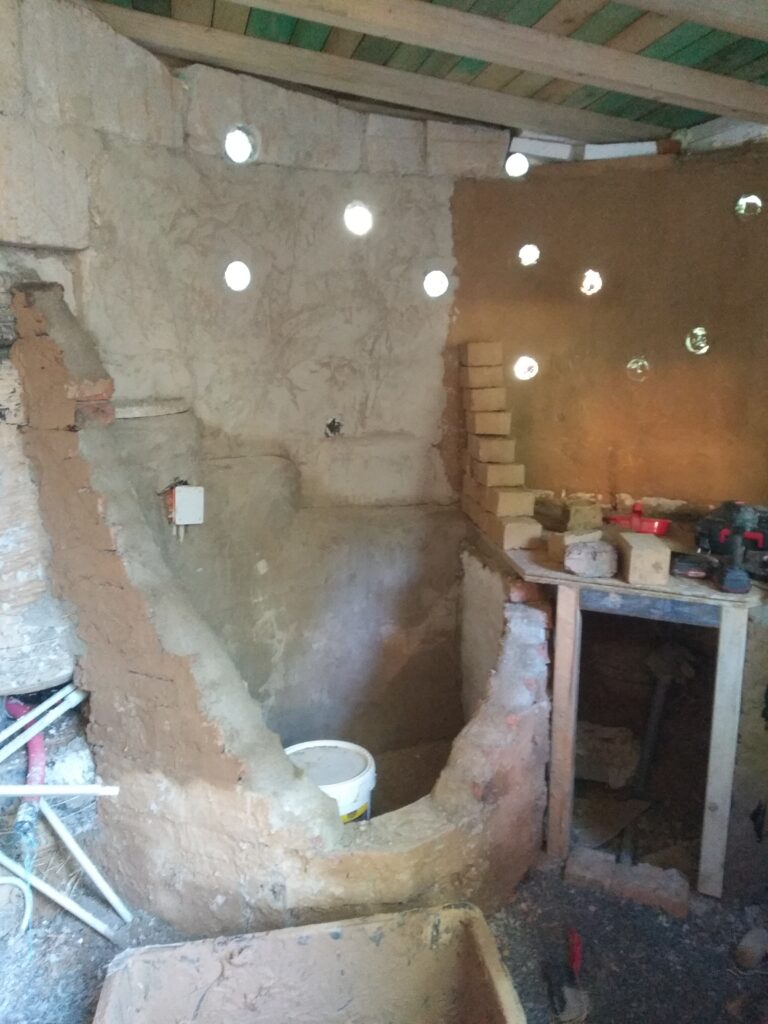